

Other conditions that can cause the belt to jump off the sheave or turn over include insufficient belt tension, significant vibrations in the drive, and shock loads. Damaged tensile cords (see above) can also lead to edge cord damage or failure.ĭuring operation, if the belt comes off the sheave or turns over, this can indicate misaligned pulleys or contamination in the drive. In extreme cases, foreign objects in the drive can damage the belt severely enough to cause breakage.Įdge cord damage is a common failure mode for V-belts.Įdge cord damage or failure can be a product of sheave misalignment, which causes the belt to track unevenly and, in some cases, twist during operation. Tensile cord damage can also occur if the belt is pried or rolled onto the sheave during installation. Damage to these load-carrying members can be caused by severe shock loads during operation or by using a belt that’s under-sized for the application. The most clear sign of accelerated belt wear or failure is a broken belt, which typically indicates that the tensile cords have been damaged. Here, we’ll look at five common ways that V-belts can fail and the most probable causes of each condition.Įxcessive loads or improper installation can lead to broken belts.
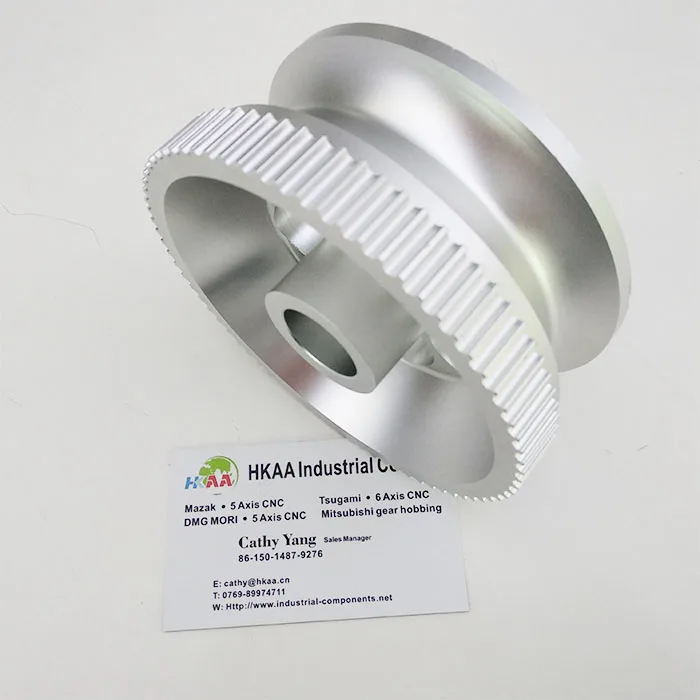
To help users determine the root cause of a failure or signs of potential failure, V-belt manufacturers provide troubleshooting guides that suggest causes and remedies for a wide range of issues. They also ensure a constant belt force, independent of belt and unit manufacturing tolerances as well as aging-, temperature-, and load-dependent belt elongation.Although there are more than a dozen symptoms of premature wear and impending failure for V-belts - ranging from visible damage to audible noise - there are a few key ways that these friction-based belts can fail during operation. They suppress belt vibrations and prevent slippage and noise. In order to safely transmit the necessary mechanical forces to drive the units in such a layout, it was necessary to introduce automatic tensioning systems in which one or more pulleys are arranged in a swiveling mechanism, spring-loaded, and damped. The need for this task was eliminated following the development of ribbed V-belts, usually with five to six ribs. Simultaneously, the requirements for the belts have risen sharply – and the performance of the auxiliaries is continuing to increase. Depending on the installation space, these components are arranged around the engine and thus determine the belt length.
#V belt pulley system designer generator
Over time, more and more units such as the water pump, power steering pump, and air conditioning generator have been integrated in the auxiliary drive mechanisms. The required belt force could only be restored by retensioning the belt via the alternator. This could cause the V-belt to squeak, for example, during rain or low temperatures. However, due to inaccurate assembly instructions, thermal expansion of the motor, and elongation of the belt over time, a drop in belt tension could occur. The required belt force was set manually by swiveling the alternator around a suspension axis. As a result, damage to the V-belt was one of the most common causes of failure in automobiles.
